Solutions
Metal products are highly diverse, and different material properties require different metal forming methods. At INGYU, we know that selecting appropriate equipment and methods based on product characteristics and carefully planned production management is crucial. This method not only improves production line utilization and product yield, but is also the key to reducing production costs and gaining competitive advantage through differentiation.
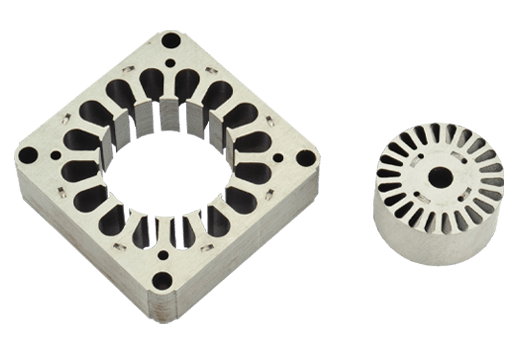
Motor Lamination
The motor core is made of stacked materials with a thickness less than 0.5mm. Minimizing stamping burrs and ensuring equal cutting surfaces are critical to improving motor efficiency. INGYU high-speed stamping with the stable bottom dead center, which helps reduce burrs and prolongs the service life of dies.
Model
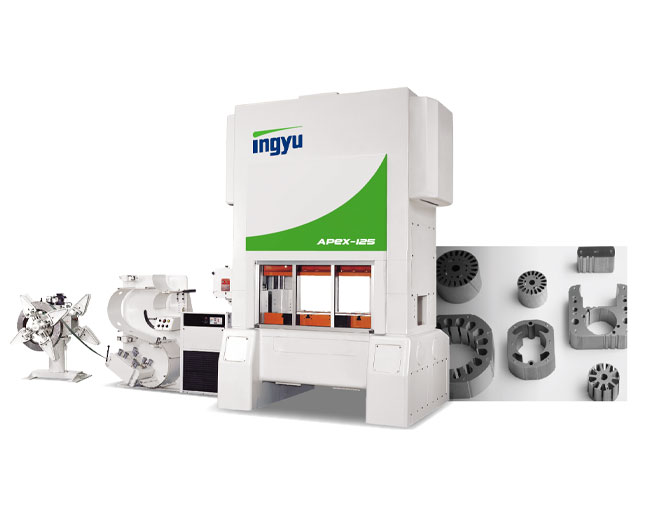
Apex-125High Speed Stamping Press
INGYU's Apex straight-side two-plunger high-speed press has been designed to meet requirements for stamped components of high accuracy. The press features two-piece casting frames. The guiding post bushings are part of the bottom frame to ensure high vertical accuracy.
Specification
Model | Apex-45 | Apex-60 | Apex-80 | Apex-125 | |
---|---|---|---|---|---|
Capacity | ton | 45 | 60 | 80 | 125 |
Stroke | mm | 30 | 30 | 30 | 30 |
Speed | spm | 900 | 800 | 600 | 500 |
Bed area | mm | 800 x 550 | 1000 x 650 | 1200 x 750 | 1400 x 850 |
Model | HV350-2400 | HV350-3000 | HV350-3700 | |
---|---|---|---|---|
Capacity | ton | 350 | 350 | 350 |
Stroke | mm | 30 | 30 | 30 |
Speed | spm | 200 - 500 | 150 - 300 | 150 - 300 |
Bed area | mm | 1800 x 1050 | 3000 x 1200 | 3700 x 1200 |